Partnering to Shape the Future of Space Exploration
The global Space Economy presents unique test and measurement projects on Earth and beyond. Interface, as a provider of mission-critical solutions, is at the forefront of partnering with others to advance discoveries.
Why do space companies and suppliers to the space industry choose Interface? It’s the precision and depth of Interface’s products. Interface has a long history as a steward for test and measurement space-related ventures, including with NASA and other space exploration companies, innovators, and space start-ups. We’ve been instrumental in supporting projects of all sizes, from educational space vehicle projects to the development of the Space Launch System (SLS).
Interface’s load cells provide highly accurate measurements, ensuring that everything from rocket structures to robotic arms can withstand the harsh environment of space. Today, Interface is one of the leading suppliers of sensor technologies used to test designs of new commercial craft, roaming planet rovers, spacewalk simulators, and advanced space robotic projects. Explore our comprehensive overview of Space Economy Solutions.
We often take for granted the immense challenges involved in space travel. Spacecraft and rockets need to withstand extreme forces during launch and operation, as outlined in The Criticality of Thrust Measurement Testing in Aerospace. Even the slightest miscalculation can have disastrous consequences. This is where Interface comes in, providing the essential force and torque testing devices to ensure space missions’ safety and success. Read: Launching into Orbit with Interface.
Interface participates annually in the industry’s leading exhibition, Space Tech Expo. We showcase products and discuss the range of sensor options with engineers when using Interface force measurement solutions. To give you insight into those discussions, the following highlights several use cases for Interface products in a wide range of space industry programs.
INTERFACE PRODUCTS ADVANCE SPACE TESTING APPLICATIONS
ROCKET STRUCTURAL TESTING
NASA’s Space Launch System (SLS) core stage will be the largest ever built, at 27 feet in diameter and 200+ feet tall. Core components, including liquid hydrogen and oxygen tanks, must withstand launch loads up to 9 million pounds-force (lbf). View the application note here.
- Marshall Space Flight Center in Huntsville, Alabama, built a 215-foot twin tower static test stand to test the 185-foot hydrogen tank. A second 85-foot test stand was built to test the oxygen tank and forward skirt.
- The test stands contain hydraulic cylinders placed strategically to push, pull, or twist the structure to produce the required loads calculated by the test engineers to simulate actual launch conditions.
- Multiple Interface 1200-series load cells with a capacity of up to 2 million lbf are attached in arrays to the hydraulic cylinders to measure the load produced by each cylinder within 0.07%.
- Load cell outputs are fed to the control system to control the cylinder forces. Temperature-compensated strain gages within each load cell reduce output errors to 0.0008%/°F (0.0015%/°C).
- Strain gages bonded to the rocket structure being tested are connected to a data acquisition system for stress analysis.
ROCKET CENTER OF GRAVITY TESTING
A space company needs to measure the center of gravity of its rocket to test its stability, control, performance, and safety objectives. The following highlights the application details, which you can also view here.
- Four 1200 LowProfile Load Cells are installed into the corners of the center of gravity testing frame.
- The rocket is placed on the frame, and the 1280 Programmable Weight Indicator and Controller gather the center of gravity results with a customized program for this application.
SPACE DOCK TESTING
A space company wants to test its spacecraft docking simulator. They wish to test the forces of the actuators used during the “lunge” when the soft capture ring is lunged forward to latch onto a space vehicle that has been mounted. They want to ensure they are working correctly when engaged and that it does not go past their overload force limit. Learn more here.
- The WTS 1200 Standard Precision LowProfile™ Wireless Load Cells are installed at the ends of the actuators. Each load cell is paired and connected to a WTS-AM-1E Wireless Strain Bridge Transmitter Module.
- The strain bridge modules wirelessly transmit force measurements to the WTS-BS-6 Wireless Telemetry Dongle Base Station when connected to the customer’s computer or the WTS-BS-1 Handheld Display for Unlimited Transmitters. Software is included for this wireless solution.
SPACE HABITAT TESTS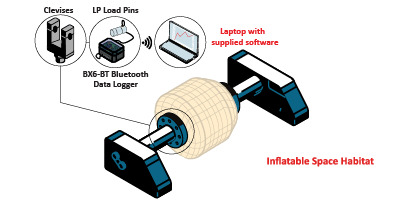
Inflatable space habitats are some of the newest innovations in the space industry. They create a new space where humans can live and work beyond the Earth’s Atmosphere. A space company wants to test the overall design and material of the inflatable habitat by conducting a burst test. Learn more here.
- Clevises and LP Stainless Steel Load Pins are embedded in the inflatable habitat’s base, where straps of heavy-duty material are woven together, creating the habitat structure. The LPs are connected to the BX6-BT Portable 6-Channel High-Speed Bluetooth Data Logger.
- The habitat is inflated, and PSI is increased slowly until the habitat bursts.
- The LPs measure the force the woven heavy-duty fabric can handle until it bursts.
- Data is wirelessly transmitted via Bluetooth from the BX6-BT Portable 6-Channel High-Speed Bluetooth Data Logger to the customer’s computer. The data can be displayed, recorded, and graphed using the supplied Log100 software. The customer also has the option to log data onto an SD Card and upload it to the computer through the SD Card.
PLANETARY SURFACE SAMPLING
As space exploration continues to grow and evolve, more robotic systems are created to collect samples of objects and materials on planetary surfaces. Robotic arms with sampling tools must be tested for scooping, drilling, and collecting samples.
- The 6A40 6-axis Load Cell is positioned between the flange and the grinder.
- 6A40 6-Axis Load Cell is linked to the BX8-HD44 BlueDAQ Series Data Acquisition System, which gathers force and torque measurement data.
- The customer connects the BXBX8’s analog outputs to their control system. This enables the customer to monitor, log, display, and graph these measurements. The results are sent to the customer’s control system via analog or digital output. Learn more here.
Interface plays a vital, though often unseen, role in space exploration by providing reliable and accurate testing equipment. Their solutions are critical for ensuring the success of missions and paving the way for a future where humanity can explore the cosmos with greater confidence.
Request a Quote from Interface, The World Leader in Force Measurement Solutions
ADDITIONAL RESOURCES
The Criticality of Thrust Measurement Testing in Aerospace
Interface Space Economy Solutions
Vertical Farming on Earth and in Space
Space Dock Capture Ring Force Testing